Para un procesador de plásticos, el tiempo del ciclo de moldeo es quizás la medida de desempeño más crítica de todas. El tiempo del ciclo de moldeo es el tiempo total requerido para moldear una descarga de plástico en el molde hasta obtener una parte terminada. De manera típica, esto incluiría el tiempo desde la inyección de plástico en el molde hasta el comienzo de la siguiente inyección de plástico. El tiempo del ciclo es dependiente del diseño del molde, la configuración de la cavidad (parte) y material que está siendo moldeado. El tiempo de ciclo total incluye el tiempo requerido para inyectar el plástico en el molde, enfriar el plástico, abrir el molde, expulsar la(s) parte(s) y volver a cerrar el molde. El tiempo de enfriamiento del material depende de las características del diseño de las líneas de enfriamiento en el molde y del espesor del material moldeado (tamaño de la pieza y geometría). El tipo de material también es un factor determinante en el tiempo del ciclo.
El tiempo del ciclo básico (teórico) está establecido para el proceso y el molde, pero el operario y las condiciones operacionales influyen en el tiempo del ciclo real alcanzado. La mayoría de las empresas sólo miden el tiempo del ciclo de moldeo de manera indirecta y después de ocurridos los hechos dividiendo el tiempo total para producir un lote de producto por el número de partes (ciclos) producidas. Eso puede ser una buena información para la contabilidad y la ingeniería, pero no tiene mucho efecto en el soporte de la gestión del trabajo y la mejora operativa.
La mejor situación consiste en medir de manera continua y presentar el tiempo del ciclo a lo largo de la jornada de trabajo. De esta manera, la alta dirección puede mantener una estrecha vigilancia sobre el desempeño real del recurso central de una planta de moldeo y asegurarse, en tiempo real, de que la planta está operando a plena capacidad.
Muchos factores contribuyen al ciclo de moldeo real incluyendo: las acciones y decisiones del operario, la condición del equipo y su mantenimiento, y las condiciones ambientales. La detección temprana de cualquier tipo de inhibidor del ciclo puede conducir a la corrección temprana y por consiguiente a un aumento en la producción.
El diseño del molde y el proceso rigen el tiempo teórico del ciclo operativo. Esto puede ser considerado el ciclo óptimo o de manera global, el mejor ciclo. Si se opera de manera más lenta que el óptimo teórico se está siendo, por supuesto, menos productivo y eficiente. Sin embargo, el hecho de que la operación sea más rápida que el ciclo diseñado no necesariamente representa algo bueno: Si el tiempo de ciclo debe ser de 11 segundos pero el trabajo actual está siendo realizado en 10 segundos, por ejemplo, puede parecer que el producto está bien cuando se encuentra en la máquina, pero éste puede fallar las pruebas de calidad más adelante en la línea de producción. El monitoreo continuo del tiempo del ciclo puede desencadenar una alerta de calidad de manera inmediata para que se verifique rápidamente la calidad del producto y para que se tomen las medidas correctivas para evitar la producción de más piezas defectuosas. Muy a menudo, la mejor práctica consiste en esforzarse para lograr la velocidad teórica – ni más ni menos- de manera consistente.
Las máquinas a las que se les ha realizado un mantenimiento adecuado serán más rápidas y más confiables, proporcionando un rendimiento más consistente. La experiencia del operador y su habilidad pueden hacer una gran diferencia en el ciclo de moldeo y por lo tanto en la productividad de la máquina y de la planta. Tener un sistema que está realizando el seguimiento histórico del tiempo del ciclo, de la gestión de los programas de mantenimiento y que es capaz de registrar lo que debería ser el tiempo del ciclo para cada máquina, es esencial para incrementar la productividad y la rentabilidad de la producción además de proporcionar una capacidad de planificación y programación mucho más adecuada.
Supongamos que un molde está diseñado para un ciclo de diez segundos; un operador de menor capacidad podría hacer funcionar la máquina en un ciclo de 11 segundos con el fin de ser capaz de mantenerse al día con sus deberes y producir buenas piezas. Ese segundo adicional en el tiempo del ciclo representa una reducción del 10% en la productividad, lo que significa que un trabajo determinado tomará un 10% más de tiempo para completarse y que el producido total de la máquina por turno se reducirá en un 10%. Llevar la máquina de nuevo a la velocidad diseñada se traduce en una mejora del 11% con respecto a la tasa reducida (dividiendo 9 segundos entre 10 para obtener el porcentaje de mejora), con el subsecuente aumento de la eficiencia y la productividad,… y el costo reducido.
Realizar el seguimiento del desempeño de moldeado (tiempo del ciclo) para cada máquina también proporciona una oportunidad para mejorar la gestión de la planta y lograr el rendimiento óptimo. Un molde determinado puede funcionar eficazmente en un ciclo de 10 segundos en una máquina, pero en un ciclo de 8 segundos en otra máquina. Si todo lo demás se mantiene igual, tal vez sería mejor ejecutar el trabajo en la segunda máquina. Teniendo en cuenta otros trabajos y sus tasas de ejecución particulares, cambios de color, las prioridades, los programas de mantenimiento, la disponibilidad del operario y otras consideraciones, es posible favorecer tareas alternativas. Estas decisiones son difíciles si no se tiene una buena información sobre el desempeño por molde/máquina/información del operario.
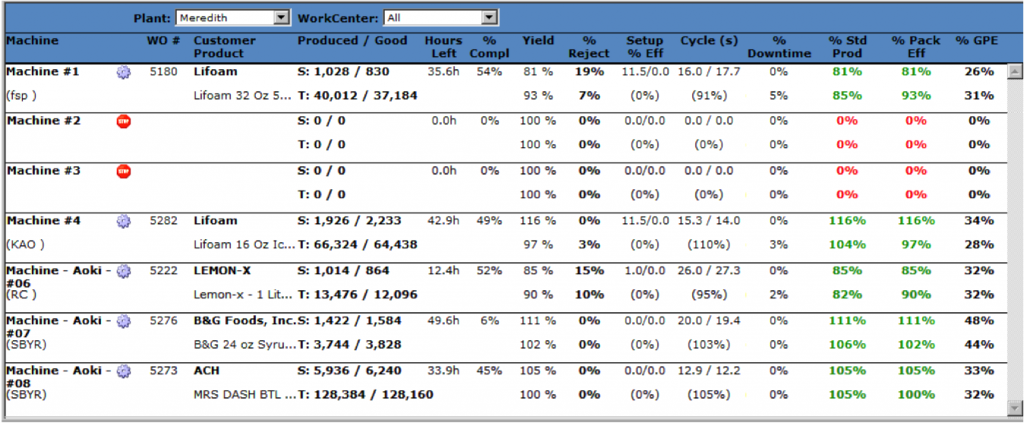
Se tiene otra oportunidad con un seguimiento constante del tiempo del ciclo en comparación con la eficiencia de empacado. El ingreso de información automatizado en el piso de producción a partir de la máquina misma, en comparación directa con el escaneo de códigos de barras de lo que está siendo empacado, puede mantener un conteo progresivo del progreso de la producción y de la calidad de la misma (rechazos). Esto proporciona datos continuos para la planificación del momento en el que se puede enviar el trabajo actual y se puede iniciar el siguiente trabajo. Adicionalmente, el seguimiento del uso de materias primas también se realiza de una manera más precisa.
En la mayoría de los casos, se pueden utilizar los sensores de monitoreo simple de la máquina que forman parte de los controles de la máquina (o que se pueden agregar a éstos) para alimentar la recopilación de datos y el análisis de funciones en su sistema de planificación y gestión. Una pequeña inversión en la recopilación de datos genera información valiosa para realizar la planificación, la operación de la planta y la gestión de la eficacia y la eficiencia de una manera más efectiva.